Columbia Partnership
The Beginnings Of A Long-Term Partnership With Columbia
Early in 2019 Vince, Beth, Dave Devine and Columbia's UK sales representative, Stephen Wilson, went on a fact-finding trip around North America to look at Columbia production plant versatility, meet the Columbia team and see block machines being made at factory HQ in Vancouver WA. A Columbia CPM+60 block machine was chosen and soon on order along with all associated batching and mixing plant with handling equipment. Despite the challenges of the COVID-19 pandemic, construction kept on track, and the plant is now up and running, finally utilising all of the available Yatton land.
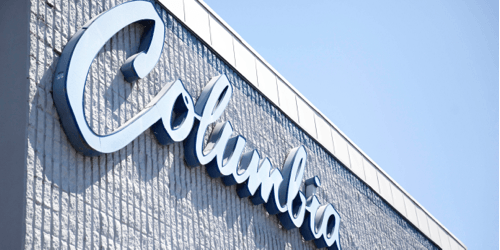
An Ultra-Modern 'State of the Art' CPM+60 Concrete Products Plant
Stowell Concrete opted for two independent sets of 4 x 40 cubic metre aggregate storage bins with feed to the bins from ground shovel dump hoppers and incline belts to a rotary conveyor. The driver selects a bin from a remote control in the shovel cab, to feed the aggregates to the bins which have high/low-level light indicators. Designed and constructed by Concrete Batching Systems Ltd in Ireland and using weighing and control automation by another Irish firm, Pneutrol International Ltd, each concrete batch is metered onto a weigh belt and conveyed to any one of three dry aggregate holding hoppers over the relative mixers.
The moisture quality check of material feeding the Columbia CPM+60 uses the latest Hydronix moisture system with real-time microwave moisture measurement sensors at the exit of all eight aggregate bins and in each mixer to sense moisture variation and compensate accordingly. With concrete cored brick, concrete coloured tumbled walling and coloured concrete block paving in mind, a Wurschum 4 "big bag" colour pigment dosing system was fitted. This allows pigment to be blended and blown to any one of the three Teka mixers, supplied by Conspare with a full set of concrete dosing hoppers and metering belts, delivering an extensive range of colour permutations along the feed belt to Columbia machine's feed drawer. Three vertical cement silos were also erected local to the mixer station to convey cementitious materials to three independent weigh vessels above each mixer, to complete the batching and mixing scope.
At the very heart of the new Stowell Concrete plant, the Columbia CPM+60 machine has a fl at steel production pallet size of 1400x700x15mm, chosen primarily due to the unique Columbia Vibration Technology (CVT) that provides controlled mould vibration, accurately guided in a completely vertical motion. The CVT results in longer mould life, uniform distribution of aggregates, reduced cement usage, precise product heights and product versatility. Columbia's patented CVT combines over 80 years of innovative engineering and field-proven capability to enable the highest quality and most comprehensive range of products in the world. The CPM+60 is an easy to operate machine with user-friendly HMI/Compact Logix control and machine adjustments made from the HMI and full menu screens for quick machine set up. In changing from product to product (including any mould change requiring a height change), the machine makes the change automatically. Product change-over is recipe driven with a push-button control and tool-less agitator and strike-off plate removal. The machine also features forced oil lubrication, a laser probe to control the feed drawer material level, full isolation between rear feed drawer section and machine centre section vibration, hydraulic linear agitation, remote valve stand, electronic product height control, product reject control and automatic mass control.
The 4 Tonne, Automatic Mould Change facility, was purchased with dual cassettes which run on a floor supported overhead monorail system. The first of the two cassettes is used to extract the mould from the machine while the second cassette offers a new mould. A mould change is very simply done from a menu-driven touch panel for different products and heights, and a complete mould change is performed in less than 4 minutes for products that are the same height
If you'd like to read more about Columbia and the new Stowell Concrete machinery click below:
https://columbiamachine.com/blog/stowell-concrete-commissions-state-of-the-art-columbia-cpm60-concrete-products-plant-at-their-yatton-hq-in-somerset-uk/